top of page
Difficile de faire plus simple : une seule pièce d'habitation et un toit plat.
Dimensions extérieures : environ 45 x 54 x 33 mm.
Quatre ouvertures dont une porte.
... et c'est tout.
Plus modeste, on peut pas.
Les murs ont une épaisseur de 3 mm.
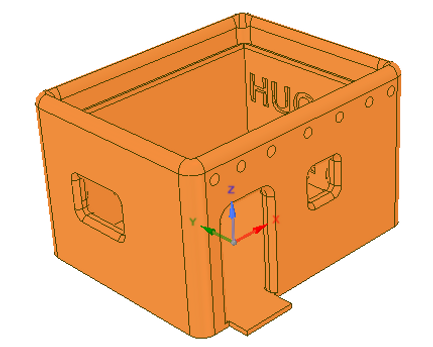

Difficile de faire plus simple : une seule pièce d'habitation et un toit plat.
Dimensions extérieures : environ 45 x 54 x 33 mm.
Quatre ouvertures dont une porte.
... et c'est tout.
Plus modeste, on peut pas.
Les murs ont une épaisseur de 3 mm.
Pour imprimer cette petite maison j'ai choisi du fil PolyWood. C'est un PLA avec du bois qui donne à la pièce un aspect "bois mat" ou "terre sèche". Facile à enduire et à peindre.
Suivant l'imprimante utilisée, il sera nécessaire de réduire au papier de verre les dimensions du toit pour qu'il s'encastre correctement et vienne en appui sur les petites nervures qui ceinturent le bâtiment à l'intérieur des murs.
Pour éviter l'affaissement des linteaux l'impression est paramétrée avec "supports d'impression", c'est à dire que les porte et fenêtres (ben oui, ya qu'une porte ! ) seront remplies d'une sorte de nid d'abeille qui supportera les linteaux au moment de leur impression.
Il faudra ensuite désoperculer toutes les ouvertures pour les débarrasser de ces supports, puis ébavurer correctement.

La maison, avec son toit, et la porte partiellement désoperculée.
Note :
Cette petite maison peut être facilement imprimée à l'échelle "N".
Il suffit, dans CURA by Dagoma, d'utiliser les mêmes fichiers ".stl" et d'appliquer le coefficient de réduction 0,54. (Hé oui ! Pas besoin de redessiner).
L'impression prendra 20 minutes et 4 grammes de PLA pour un coût matière de l'ordre de 0,20€ !
Si l'échelle 1:43 vous tente, il suffit d'appliquer un coefficient x2 dans CURA.
Il faudra 5 heures d'impression et 73 grammes de PLA (moins de 4€).
C'est encore jouable.
Ah ! petite remarque : le bâtiment est marqué "HUGO 2017" à l'intérieur.
Mon petit fils voulait que "son œuvre" soit signée ! (c'est la seule chose que j'ai faite sur ce modèle).
Téléchargements :

Petite maison en adobe
Un de mes petits fils voulait absolument dessiner et imprimer une maison en 3D.
J'ai orienté son choix vers un modèle simple : une petite maison de paysan modeste de la région de Santa Fe, en adobe, qui va me servir sur mon réseau. Tant qu'à faire...
Nombre de visites :
316
Jauges AWG
Les lois fondamentales en électricité
Jauges AWG
La loi d'ohm : U = R x I
U : la tension s"exprime en Volts R : la résistance s'exprime en Ohms I : le courant s'exprime en Ampères
Un fil conducteur transportant un courant électrique (I) oppose une certaine résistance (R) au passage du courant.
Cette résistance (R) sera d'autant plus grande que le fil sera fin et long.
On peut calculer la résistance d'un conducteur : R = rho x L / s
R : résistance en Ohms rho = 17 x10 -9 pour le cuivre L : longueur du fil en m s : section du fil en mm²
⇒ Plus le fil sera gros, moins il offrira de résistance au passage du courant
La puissance dissipée : P = U x I ou par transformation : P = R x I²
(P : la puissance s'exprime en Watts).
L'effet Joule : W = R x I² x t
W : énergie (chaleur) dissipée en joules t : temps de fonctionnement du circuit en secondes.
⇒ Plus le fil sera gros, moins il s'échauffera.
Notion de résistance de contact
Lorsque vous connectez deux fils ensemble, ou un fil dans une borne, ou deux rails via un éclisse, etc . . .
... il apparaît au raccord de ces deux conducteurs une résistance de contact due principalement
à l'oxydation et à la faible surface de contact des métaux en présence.
Pour diminuer cette résistance, il faut :
-
souder les conducteurs l'un à l'autre ;
-
utiliser des connecteurs de bonne qualité.
Table de conversion AWG en mm²
AWG (American Wire Gauge) est une manière d'exprimer la section des fils.
Vous trouverez souvent ce type d'expression dans les fils et câbles destinés à l'électronique.
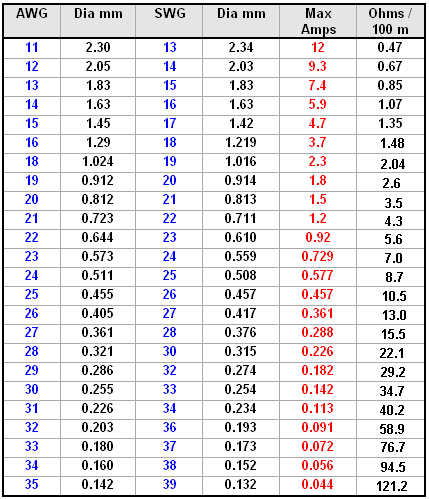
Table de conversion AWG en mm²
AWG (American Wire Gauge) est une manière d'exprimer la section des fils.
Vous trouverez souvent ce type d'expression dans les fils et câbles destinés à l'électronique.
Exemple :
Si I = 1 A et longueur du fil = 10 m : nous aurons une chute de tension aux bornes de ce fil : U = R x I
-
AWG 26 = 1.34 V
-
AWG 22 = 0.53 V
-
AWG 15 = 0.10 V
C'est à dire que la chute de tension dans un fil AWG 15 est 13 fois moindre que dans un fil AWG26.
Nous voyons donc l'intérêt d'utiliser des fils de section la plus importante possible.

Résistivité des matériaux (rho) en Ohms . m
Ce qui veut dire que nos rails en Maillechort (Cu - Ni - Zn) offrent une résistance 18 fois supérieures au Cuivre.
Il est donc intéressant de connecter ces rails le plus fréquemment possible à l'alimentation électrique (Bus).
Vous voyez aussi la très mauvaise conductivité de
l'association Maillechort (rails) avec l'inox (éclisses).
Dénuder du fil vernis
Dénuder du fil verni
Nous avons parfois besoin de dénuder du fil vernis ou d'étamer du fil de cuivre vernis de très petit diamètre.
C'est le cas des fils des bobinages de moteurs d'aiguillages ou de certains transformateurs miniatures.
Certaines LED's que nous utilisons pour les feux des locos ou les feux de fin de convoi sont équipées d'origine de fils de cuivre très fins.
Dans tous les cas, le dénudage de fil vernis aussi fin par grattage est un problème délicat voir impossible.
Une solution existe : l'aspirine ou acide acétylsalicylique !
La photo ci-dessous vous montre comment procéder :
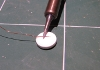

Nettoyer proprement la panne du fer à souder et remettez à peine de soudure à l'étain.
Ensuite vous coincez le fil -- sans trop appuyer : le fil est fragile -- entre l'aspirine et la panne du fer.
Tirer délicatement le fil sous la panne : au final le fil est dénudé ET étamé.
Au cours de l'opération le cachet d'aspirine va noircir et fondre. Après plusieurs utilisations il prendra l'aspect ci-dessous :
ATTENTION : cette méthode pour dénuder ou étamer du fil vernis ne fonctionne, et n'est utile, que pour des fils de petit diamètre (moins de 0,2mm).
SECURITE : Evitez de respirer les vapeurs qui se dégagent au cours de l'opération de dénudage du fil de cuivre. Je ne suis pas sûr quelles soigneraient vos maux de tête !
En règle générale, chaque fois qu'une manipulation provoque ou risque de provoquer des projections, un dégagement de fumées, de vapeurs ou de poussières, il faut porter des protections adaptées -- lunettes, masque anti-poussières -- et travailler dans un endroit aéré.
N.B. Un collègue me signale que la méthode ne fonctionne pas avec certains vernis conçus pour résister à des températures élevés.
Eau à souder
L'EAU à SOUDER
En modélisme ferroviaire on est amené à souder des rambardes, des caténaires, des barrières, des échelles ou des pylônes.
Pour cela nous devons réaliser des soudures très légères, avec très peu d'apport d'étain.
La méthode de soudage des composants électroniques ne permet pas d'obtenir des soudures assez discrètes.
L'utilisation d'un autre décapant et d'une autre méthode de soudage s'imposent.
Matériel nécessaire :
-
acide chlorhydrique du commerce (magasins de bricolage) ;
-
tôle de zinc pur que vous découperez en morceaux de 1 à 2 cm² (pas de la tôle d'acier zinguée). Vous en trouverez chez votre plombier-zingueur ;
-
une bouteille en verre de 1 litre ;
-
des gants de caoutchouc (gants de cuisine par exemple) ;
-
des lunettes de protection ;
-
un seau rempli d'eau pour laver abondamment les éventuelles projections de produit.
Précautions :
SAFETY FIRST ! SECURITE D'ABORD !
ATTENTION ! l'acide chlorhydrique est un produit dangereux qui peut occasionner de très graves brûlures !
La réaction chimique de l'acide sur le zinc provoque un dégagement d'hydrogène et de vapeurs chlorées, nocives et très oxydantes.
Il faut donc impérativement travailler à l'extérieur, d'une part pour votre santé et d'autre part pour ne pas faire rouiller tous vos outils dans l'atelier, croyez-en mon expérience !
La réaction est exothermique et peut provoquer un échauffement important de votre récipient en verre et de son contenu (jusqu'à ébullition !) si vous introduisez les morceaux de zinc en trop grande quantité à la fois.
Comment procéder ?
-
enfilez les gants en caoutchouc et mettez vos lunettes ;
-
verser avec précaution 1/2 litre d'acide chlorhydrique dans le flacon de verre ;
-
ajouter les morceaux de zinc, un par un. La réaction d'attaque du zinc se manifeste par un dégagement gazeux ET une élévation de la température. Attendre l'attaque complète avant d'ajouter le morceau de zinc suivant ;
-
lorsqu'il vous semble que le zinc n'est plus attaqué (plus de dégagement gazeux), ajouter 3 ou 4 morceaux de zinc et laisser le flacon dans un endroit où il ne risque pas d'être renversé, toujours à l'extérieur, pendant 15 jours. (sans le fermer) ;
Après 15 jours, examiner la solution :
-
si les copeaux de zinc ont été complètement attaqués, rajouter un ou deux morceaux et... attendre encore au moins 8 jours. Il doit rester un peu de zinc au fond du flacon, preuve que l'attaque est "à saturation".
Pourquoi attendre si longtemps ?
Lorsqu'il semble que la réaction est achevée (plus de dégagement gazeux) en réalité il reste encore des traces d'acide chlorhydrique dans la solution.
Ces traces -- si on ne les élimine pas -- provoqueront un ternissement des soudures et une attaque du laiton ou du cuivre des pièces soudées qui se matérialisera par l'apparition de cristaux de sels blancs (et corrosifs).
D'autre part, dans cet état, l'eau à souder reste corrosive aussi pour les doigts !
Grâce à une réaction d'attaque menée "jusqu'à saturation" la solution ne comportera plus trace d'acide chlorhydrique.
Cela ne signifie aucunement qu'il ne faut pas manipuler la préparation d"eau à souder avec précautions. Il en va de même avec tout produit chimique
-
lorsque l'attaque aura été menée à son terme, dans le fond du flacon il y aura un dépôt d'aspect terreux clair. C'est normal. Eviter d'agiter le flacon lors de sa manipulation pour ne pas re-mélanger ce dépôt ;
-
transvaser le liquide dans des récipients plus petits, en verre ou en plastique, mais avec des bouchons plastiques qui ferment correctement (ni liège, ni métal).
Votre préparation d'eau à souder est prête à l'emploi.
Il s'agit d'une solution aqueuse de chlorure de zinc ZnCl2, celle-là même que nos pères et grands-pères préparaient pour souder les parties en zinc des toitures et les collecteurs d'eau de pluie.
Il ne faut SURTOUT PAS FILTRER la solution.
En effet, les solutions aqueuses de chlorure de zinc ont la propriété de dissoudre l'amidon, la soie et la cellulose.
Une filtration provoquerait une perte d'efficacité du produit si ce n'est sa destruction.
Utilisation de l'eau à souder :
-
déposer une toute petite goutte d'eau à souder sur les pièces à assembler à l'aide d'un petit pinceau en poil synthétiques ou avec une tige de laiton ;
-
nettoyer le fer à souder et apporter de nouveau une toute petite quantité de soudure fraîche sur la panne. La résine décapante disparaît en fumée, mais c'est sans importance ;
-
approcher la panne au contact des pièces à souder : sous l'action de la chaleur le ZnCl2 provoque le décapage des pièces à souder. Aussitôt l'étain contenu sur la panne "coule" et forme la soudure ;
-
il est tout de même recommandé de laver les soudures à l'eau, de façon à éliminer toute trace de ZnCl2.
Pour éliminer un excès de soudure :
-
remettre une petite goutte d'eau à souder sur la soudure en question ;
-
nettoyer soigneusement le fer ;
-
toucher la soudure avec la panne : la soudure en excès "monte" sur la panne ;
-
recommencer l'opération si nécessaire.
Remarques :
J'utilise depuis deux ans une eau à souder préparée "à saturation".
⇒ Je n'ai jamais lavé une seule soudure et à ce jour aucune d'elle ne s'est ternie.
Aucune cristallisation saline n'est apparue.
Amateurs de trains miniatures, lorsque vous aurez essayé l'eau à souder, sûr, vous ne pourrez plus vous en passer !
Section fils cablage
CABLAGE : étude de la section des fils
Vous trouverez dans cet article une étude sommaire concernant les pertes dans les conducteurs d'alimentation "traction" et leurs impacts, pour un réseau de trains miniatures de conception modulaire.
Dans le cas d'un réseau fixe, non modulaire, l'étude reste valable : il suffit de ne pas tenir compte des résistances dans les contacts des connecteurs inter-modules, R3 et R8.
Cette étude est applicable aussi bien à un câblage DCC qu'à un câblage analogique.
1.- Consommation des convois
2.- Section minimale des conducteurs
3.- Réflexions sur les pertes admissibles
4.- Résistance du câblage : inventaire rapide et analyse
1.- Consommation des convois :
Typiquement, une machine en HO consomme entre 600 mA et 1000 mA sous 12 Volts
Le moteur consomme donc "comme" une résistance de 12 Volts/0,6 A soit 20 Ohms
et pour certains moteurs RIVAROSSI : 12 V/1 A soit 12 Ohms
(NDLR : ces raccourcis vont me valoir les foudres de mon prof d'électrotech !!!)
Si on envisage une traction en unités multiples :
-
les consommations s'établissent respectivement à 1800 mA et 3000 mA
-
les résistances équivalentes sont alors de l'ordre de 6,6 Ohms et 4 Ohms
Cette estimation ne prend pas en compte la consommation supplémentaire induite par les éclairages des machines et des voitures.
Pour l'instant nous pouvons négliger ce point compte tenu de la faible consommation des LED's
En conclusion, le cas le plus défavorable (mais pas improbable) est donc celui d'un convoi en UM avec trois machines gourmandes :
Consommation :
Im = environ 3000 mA
Résistance équivalente des moteurs :
Rm = environ 4 Ohms
Puissance correspondante :
Pm = environ 36 Watts
2.- Section minimale des conducteurs :
Pour les conducteurs en cuivre avec des isolants standards, on admet un courant de travail maxi
de 5 à 7 A/mm².
Au delà les conducteurs chauffent trop et les isolants risquent d'être détruits, particulièrement si les conducteurs en question sont enroulés ou disposés en paquets.
Décidons de fixer la limite à 6 A par mm².
Plaçons nous dans le cas défavorable exprimé ci-dessus, càd une consommation maximale,
soit environ 3000 mA
⇒ la section minimale des fils de câblage ne doit donc pas être inférieure à 0,5 mm²
3.- Réflexions sur les pertes admissibles :
Un usage (et peut-être même une règle) en électrotechnique établit que les pertes dues aux conducteurs qui alimentent un appareil ne doivent pas dépasser 5% de sa puissance.
Plaçons nous dans le cas le plus exigeant :
Consommation
Im = environ 3000 mA
Résistance équivalente des moteurs :
Rm = environ 4 Ohms
⇒ Puissance correspondante : Pm = environ 36 Watts
⇒ 5% de 36 Watts = 1,8 Watts
Puissance perdue «admissible» dans les fils : Pp = 1,8 W
L'ensemble du câblage ne doit donc pas occasionner des pertes supérieures à 1,8 W
Soit une résistance de câblage maxi de : Rc = Pp / Im² càd Rc = 1,8 / 3²
Rc = 0,2 Ohms
⇒ la résistance totale du câblage ne doit donc pas dépasser 0,2 Ohms
Pour se rassurer un peu :
Si on admet que jamais on ne fonctionnera en UM à 3000 mA mais seulement en unité simple avec rame éclairée, soit une consommation maxi de 1000 mA alors les paramètres sont les suivants :
Im = environ 1000 mA
Rm = environ 12 Ohms
⇒ Pm = environ 12 Watts
⇒ Pp = 0,6 Watts (Perte admissible)
Soit une résistance de câblage maxi de : Rc = Pp / Im²
Rc = 0,6 / 1² = 0,6 Ohms
⇒ résistance totale maximale du câblage = 0,6 ohms
... ce qui n'est pas beaucoup !!!
Constatation : (et pour faire simple)
La résistance TOTALE du câblage ne doit pas être plus grande que 5% de la résistance équivalente du (ou des) moteur(s).
4.- Résistance du câblage : inventaire rapide et analyse :
Le tableau ci-dessous donne un aperçu de la chaîne des éléments qui constituent la résistance totale du câblage d'un réseau.
Ce tableau n'est pas exhaustif (il serait inutilement trop complexe). (j'ai omis par exemple la résistance d'un éventuel fusible de protection)
Il suffit à nous faire comprendre les points à travailler lors d'un câblage.


Reste à considérer les résistances des fils de câblage :
Rappelons les limites déterminées plus haut :
Section minimale pour un courant de traction de 3000 mA : 0,5 mm²
Section minimale pour un courant de traction de 1000 mA : 0,2 mm²
Résistance totale du câblage pour 3000 mA : maxi0,2 Ohms
Résistance totale du câblage pour 1000 mA : maxi0,6 Ohms
Pour fixer facilement les idées :
Un conducteur cuivre de section 1mm² et de longueur 1mètre
présente une résistance de 0,017 Ohms
Voyons les choses sous un autre angle :
Un conducteur de 0,2 Ohms c'est :
environ 3 mètres pour une section de 0,2mm²
environ 6 mètres pour une section de 0,5mm²
environ 15 mètres pour une section de 1mm²
environ 20 mètres pour une section de 1,5mm²
environ 30 mètres pour une section de 2,5mm²
Un conducteur de 0,6 Ohms c'est :
environ 7 mètres pour une section de 0,2mm²
environ 20 mètres pour une section de 0,5mm²
environ 35 mètres pour une section de 1mm²
environ 50 mètres pour une section de 1,5mm²
environ 85 mètres pour une section de 2,5mm²

N'oublions pas que, lorsqu'on parle de la longueur des conducteurs de câblage,
il s'agit de la longueur du fil "ALLER" + la longueur du fil "RETOUR"
⇒ autrement dit, pour un réseau modulaire non bouclé qui se développe sur 20 mètres depuis le tableau de commande, la longueur des conducteurs à prendre en considération dans les calculs est 40 mètres.
Conséquences :
Si on se fixe comme impératif de pouvoir fonctionner en UM avec un courant traction de 3000 mA ou de permettre la circulation simultanée de 3 convois éclairés avec des moteurs gourmands (ce qui est plus que probable sur un réseau de grande taille), alors un bus d'alimentation en section de 2,5 mm² ne suffit même pas.
Si on décide que jamais plus d'un seul convoi ne sera en cours de déplacement, alors un bus d'alimentation de section 1,5mm² sera suffisant. (mais pas moins).
Remarque :
Que l'on fasse circuler une ou plusieurs machines simultanément sur le réseau, les conducteurs d'alimentation auront une forte section et donc une capacité en courant très nettement supérieure à ce qu'on leur demande.
Ce n'est pas un paradoxe.
C'est même une propriété qui va être utile.
Voyons les choses d'encore une autre manière :
L'ensemble des fils de câblage se décompose ainsi (on néglige les résistances des contacts dans les switchs et les connecteurs) :

Le cas du bus d'alimentation est réglé : les conducteurs R4 et R7 seront de forte section
Qu'en est-il de R1 et R10 d'une part et de R5 et R6 d'autre part ?
Les fils qui vont des connecteurs sous les modules, jusqu'aux rails sont relativement courts : longueur de R5 + longueur de R6 inférieure à 1 mètre, c'est à dire :
-
une résistance maximale de 0,085 Ohms pour une section de 0,2 mm²
-
une résistance maximale de 0,034 Ohms pour une section de 0,5 mm²
Il en est de même pour les longueurs totales des fils d'alimentation à l'intérieur du tableau de commande et de répartition :
Longueur de R1 + longueur de R10 inférieure à 2 mètres, c'est à dire :
-
une résistance maximale de 0,170 Ohms pour une section de 0,2 mm²
-
une résistance maximale de 0,068 Ohms pour une section de 0,5 mm²
Conséquences :
Les valeurs de résistance cumulées pour R5 + R6 + R1 + R10 sont de :
environ 0,100 Ohms pour 3 m de fils de section 0,5 mm²
environ 0,250 Ohms pour 3 m de fils de section 0,2 mm²
Si on met en parallèle ces valeurs avec celles du bus d'alimentation, on voit qu'il est possible d'utiliser des sections plus faibles pour les parties de câblage sous les modules ou dans les pupitres de commande et de répartition.
En effet :
8 mètres de fil en section 0,5 mm² ont la même résistance que 40 mètres en 2,5mm² !
Donc, quand les câblages sont courts, l'impact d'un fil de petite section est minime.
Remarque :
L'emploi de fil de section 0,2 mm² est fortement déconseillé.
Il ne convient pas pour des courants supérieurs à 1000 mA, mais surtout – on vient de le voir – sa faible section occasionne des chutes de tension trop élevées.
Un câblage des pupitres et des liaisons BUS D'ALIMENTATION / RAIL réalisé en 0,2 mm² présente déjà une résistance cumulée de l'ordre de 0,250 Ohms ce qui n'est pas négligeable vis-à-vis des valeurs limites 0,2 ou 0,6 Ohms dont ont parle plus haut.
Le fil de 0,2 mm² doit donc être réservé à des liaisons extrêmement courtes, de l'ordre de quelques dizaines de centimètres maxi, et uniquement quand on ne peut pas faire autrement.
Dès que la place disponible le permet, il faut passer en 0,5 mm².
En conclusion :
Ce qui est à considérer lorsqu'on calcule les sections de fils pour le câblage d'un réseau miniature ce n'est pas la capacité des conducteurs à transporter un courant donné mais bien plutôt les pertes occasionnées en fonction des longueurs de câblage.
La bonne nouvelle, c'est que, pour raccorder les alimentations sur les rails, il suffit de morceaux de fils de quelques centimètres en section 0,2 à 0,5 mm², soudés d'un côté au rail et de l'autre aux fils de forte section du bus traction.
Ceci permet des soudures discrètes sans pénaliser la qualité électrique du câblage.
Calcul des LED
CALCUL DES LED
Applications ANDROÏD gratuites :
LED Resistor calculator
ElectroDroïd : très complète.Géniale !
Site de calculs "en ligne" :
http://ledcalc.com/
http://www.ohmslawcalculator.com/led-resistor-calculator
http://www.hobby-hour.com/electronics/ledcalc.php
Petits tableaux rapides :


Cuve gravage PCB
Petite cuve pour gravage PCB
Mis à jour le 18/07/2020
La plupart des mes circuits imprimés mesurent moins de 60 x 40 mm.
La cuvette de gravage que j'utilisais jusqu'à présent mesure 240 x 160 mm.
Quand elle est remplie avec 200 ml de produit (1/5ème de litre), il n'y a QUE 5 mm d'épaisseur de liquide.
C'est assez peu compte-tenu des bossages au fond de la cuvette et le circuit est mal immergé.
Dans ces conditions il est même quasiment impossible de graver proprement des circuits imprimés double face.
Et au final, si je n'ai que 3 ou 4 PCB à graver, je jette 200ml de produit qui n'étaient pas encore épuisés.
Voici une petite cuve de 128 ml, et qui est pratique pour les PCB double face :

Elle est constituée de seulement 5 pièces de plexi, collées avec un mastic-colle universel (de chez AYRTON par exemple - pub gratuite).
Cotes intérieures : 10 mm x 160 mm.
Cela dit la seule chose importante ce sont les gravages des repères de remplissage à 40, 60 et 80 mm (ou tout autre gravage qui respecte les proportions ci-dessus).
Ce gravage permet de remplir la cuve sans être obligé de recourir à un gobelet doseur.
Les repères sur cette dimension de cuve correspondent à un mélange composé de :
-
2 parts d'eau, soit 64 ml ;
-
1 part d'acide chlorhydrique à 23%, soit 32 ml ;
-
1 part d'eau oxygénée à 130 volumes, soit 32 ml (peroxyde d'hydrogène).
... totalisant 128 ml de produit.
ATTENTION : le peroxyde d'hydrogène et l'acide chlorhydrique sont des produits dangereux.
Soyez conscient des dangers lorsque vous manipulez ces produits. Utilisez les protections adaptées (lunettes, gants) et travaillez en extérieur.
En effet, l'attaque des PCB s'accompagne d'un dégagement de chlore. Désagréable et dangereux à respirer mais aussi très oxydant pour les outils de l'atelier !
Remarque de mon camarade Alain :
Ces proportions de mélange correspondent à un bain "rapide". L'attaque se fait en 30 à 90 secondes suivant l'usure et la température du bain.
On peut utiliser un mélange plus "lent" :
-
2 ou 3 parts d'eau,
-
1/2 part d'acide chlorhydrique, soit 16 ml
-
1/2 part d'eau oxygénée, soit 16 ml
... c'est à dire des quantités plus faibles de produits.
L'attaque se déroule en 3 à 5 minutes suivant l'usure du bain. La capacité de gravage du bain est réduite : le bain est plus vite épuisé puisqu'il y a moins de produit actif.
Pour un mélange avec 3 parts d'eau j'ai gravé des repères sur l'autre face de la cuve, respectivement à 10, 20 et 80 mm du bas.
Réalisation de la cuve : elle ne comporte aucune difficulté majeure.
La vue éclatée ci-dessous montre les cinq pièces de la cuve :

-
les deux flancs sont taillés dans du plexi de 3mm ;
-
le reste est fabriqué dans du plexi de 5 mm.
Pour garantir une bonne accroche du mastic il est indispensable de dépolir soigneusement les surfaces qui vont être en contact.
-
on commence par assembler les deux flancs avec les deux entretoises. Laisser le mastic durcir pendant 24 heures ;
-
après avoir vérifié – et au besoin rectifié – le bon équerrage de l'assemblage, coller la cuve sur son socle et laisser durcir 24 heures.
Il faut être un tout petit peu généreux sur la quantité de mastic-colle de façon à éviter les fuites.
Petite remarque : le trait supérieur pour le niveau du bain d'attaque est à 20 mm du haut de la cuve.
Il n'est pas raisonnable de remplir d'avantage la cuve.
En effet, lors de l'attaque avec le mélange "rapide" il y a un fort dégagement de bulles qui fait monter le niveau du liquide et risque de le faire déborder.
Un remplissage à 80 mm est un grand maximum.
Rien n'empêche de construire une cuve plus haute (120 mm par exemple).
Avec le mélange qualifié de "lent" (voir plus haut) les bulles sont plus fines et moins abondantes. Le phénomène est moins gênant.
Ajouté en avril 2014 :
Jacques, mon camarade de club, toujours très prudent et soucieux de la sécurité, utilise une astuce que je vous conseille d'adopter : il installe la cuve à graver dans un dessous de pot de fleurs.
Ainsi, en cas de débordement, le bain d'attaque est confiné dans le dessous de pot et ne provoque aucun désagrément à la table de travail. On a tout le temps d'aller nettoyer l'ensemble à grande eau.
Merci Jacques.
Ajouté en juin 2015 :
Depuis le 2 septembre 2014, suite à l'évolution de la réglementation européenne, l'eau oxygénée à 130 volumes (32 à 35%) est considérée comme un "précurseur d'explosifs". Elle n'est plus en vente dans les grandes surfaces. Elle est réservée aux professionnels qui montrent patte blanche.
Journal officiel de l'Union Européenne.
Actuellement on ne trouve plus dans le commerce "grand public" que de l'eau oxygénée à 12% (au lieu de 35%).
Cela signifie qu'un litre d'eau oxygénée à 12% contient à peu de choses près 3 fois moins de H2O2 qu'un litre d'eau oxygénée à 35%... et 88% d'eau.
Ceci oblige à reconsidérer les proportions du mélange destiné à l'attaque de nos circuits imprimés.
Un mélange d'attaque "rapide" sera donc constitué ainsi :
-
1 part d'acide chlorhydrique à 23%, soit 30 ml ;
-
3 parts d'eau oxygénée à 12%, soit 90 ml.
-
.. et c'est tout. En effet, l'eau nécessaire est DÉJÀ dans l'eau oxygénée du commerce !
(Au passage, je vous laisse calculer le prix de l'eau en question...).
Un mélange d'attaque "lent" comportera une petite addition d'eau... du robinet celle là :
-
1 à 2 parts d'eau, soit environ 20 ou 40 ml ;
-
1 part d'acide chlorhydrique à 23%, soit 20 ml ;
-
3 parts d'eau oxygénée à 12%, soit 60 ml.
Total : 100 à 120 ml de mélange pour une cuve qui peut en contenir au maximum 128 ml.
Ah ! encore une petite chose très importante : pour éviter des projections dangereuses il ne faut jamais verser de l'eau dans l'acide, mais verser l'acide dans l'eau.
Dans notre cas il faudra préparer le mélange en versant l'acide chlorhydrique dans l'eau oxygénée à 12%, donc 88% d'eau.
Remarque : le gravage des repères de niveau sur la cuve reste valable (première image de l'article).
En effet, les 60 premiers millimètres prévus initialement pour H2O et HCl seront occupés par l'eau oxygénée à 12%, et les 20 mm supérieurs par l'acide chlorhydrique à 23%.
Les caractéristiques résumées de la cuve :
-
dimensions intérieures : 10 x 100 x 160,
-
quantité de liquide : environ 128 ml,
-
capacité de gravage avant épuisement du bain :
- environ 300 cm² (avec le mélange "rapide"),
- environ 150 cm² (avec le mélange "lent"), -
dimensions maximales du PCB : environ 80 x 160 mm,
Un autre intérêt de cette cuve c'est la position verticale du circuit dans le bain d'attaque : le dégagement gazeux abondant remonte le long du circuit et évite la stagnation de bulles sur les trous des pastilles. La qualité finale du PCB n'en est que meilleure.
Ceci ne dispense pas d'agiter un peu le PCB dans le bain.
L'élévation de température provoquée par la réaction d'attaque dispense aussi de réchauffer le bain.
Ah ! j'oubliais...
Comment maintenir le circuit en cours d'attaque ?
Dans la mesure où je ne produis que quelques exemplaires de circuits à chaque fois, j'ai rejeté toutes les solutions du genre "support réglable".
-
un tel support est délicat à construire ;
-
son encombrement limite la taille maximale des circuits que pourrait accepter la cuve. Il conduit donc à prévoir une cuve plus grande avec pour conséquence une plus grande consommation de liquide d'attaque
-
il oblige à prévoir un système d'agitation du liquide pour éviter la stagnation des petites bulles dans les trous des pastilles, ce qui augmente encore la taille de la cuve pour une même taille maximale de circuit imprimé.
J'ai opté pour un simple crochet formé au bout d'un morceau de fil électrique isolé, diamètre 0,5 mm et longueur 10 à 15 cm.
-
avant gravage je perce un petit trou de diamètre 2 à 3 mm sur le bord de la plaque de PCB, dans une zone excédentaire ;
-
ensuite je suspends le PCB au crochet et je le trempe dans le bain... et j'agite à la main.
Simple, efficace, facile à nettoyer, et les doigts ne sont jamais en contact avec le liquide du bain d'attaque.
Que demander de plus ?
La transparence des deux faces de la cuve permet de voir quand l'attaque est à son terme.
Encore plus petit !
Les circuits imprimés embarqués dans le matériel roulant ferroviaire miniature ou dans les véhicules "Car Faller" à l'échelle HO mesurent souvent moins de 30 x 40 mm. Certains d'entre eux ont une taille inférieure à 18 x 18 mm.
En général le tirage se limite à deux ou trois exemplaires d'un même circuit.
J'ai donc fabriqué sur le même principe une deuxième cuve, plus petite et plus économe en produits.
-
dimensions intérieures : 10 x 70 x 70 ;
-
quantité de liquide : environ 35 ml, (remplissage à 50 mm maxi), dont 9 ml d'acide
et 9 ml d'eau oxygénée ; -
capacité de gravage avant épuisement du bain : environ 80 cm² de circuit cuivré ;
-
dimensions maximales du PCB : environ 45 x 60 mm.
PCB et impression LASER
«Bof ! Encore une méthode de plus» allez-vous dire.
Exact.
Il suffit en effet de chercher un peu sur le net pour découvrir deux douzaines de méthodes de transfert d'un typon sur le cuivre d'un PCB, à partir d'une impression LASER, chaque méthode ayant sa particularité :
-
utilisation de couvertures de magazines en papier glacé ;
-
PNP Blue ;
-
laminage avec une plastifieuse modifiée ;
-
nettoyage à l'acétone ou à l'alcool ;
-
etc., etc.
Bien sûr j'ai essayé chacune des méthodes... avec plus ou moins de réussite... plutôt moins que plus d'ailleurs.
Dans le meilleur des cas on n'a que quelques manques et des pistes échancrées :

Parfois – trop souvent à mon goût – plusieurs pistes sont coupées.
Bref ! les résultats sont très inconstants et pour tout dire assez décevants.
De plus le papier glacé n'a pas une qualité égale d'un magazine à l'autre – c'est une des causes de l'inconstance des résultats – et il fait courir un risque sérieux à l'imprimante (risque d'endommager le fil corona ou le cylindre).
Je me suis appuyé sur les différentes méthodes dénichées sur le net, en français et en anglais, en prenant le meilleur de chacune... et j'ai tiré profit des hasards heureux de certaines manipulations.
J'ai enfin obtenu ce que j'espérais :
-
des résultats constants et reproductibles ;
-
quasiment jamais de ratage ;
-
pas d'outillage particulier (genre "plastifieuse" ou imprimante modifiée) ;
-
utilisation de PCB non pré-sensibilisé ;
-
possibilité de réutiliser le PCB avec la même technique en cas de ratage.
Remarque : cette méthode n'est applicable que si les PCB sont plus petits que la semelle du fer à repasser dont vous disposez.
1°- Impression du typon :
Pour obtenir des résultats constants sans faire courir de risques à l'imprimante il faut utiliser un support d'impression prévu pour imprimante laser.
Oui, il y a le PNP blue.
Cher.
En fait il suffit d'imprimer le dessin du circuit sur un papier photographique pour imprimante laser, brillant et le moins épais possible.
Celui que j'utilise est du papier brillant recto-verso en 150 grammes.

Prévoir un supplément de papier pour permettre
la manipulation du typon et du PCB après le laminage :
ainsi, à toutes les étapes, on évite de poser les doigts sur le typon ou de se brûler avec le PCB qui sera très chaud.
2°- Décapage du cuivre :
Simple : de la laine d'acier triple zéro et de l'huile de coude.
-
mettre le cuivre à nu en le polissant par passes croisées. La laine d'acier triple zéro ne provoque pas de rayures néfastes sur le cuivre ;
-
lorsque le cuivre est correctement poli on le débarrasse des poussières d'acier par soufflage.
Pas d'alcool qui ne dégraisse pas si bien que cela.
Pas d'acétone, qui est toxique, très volatile et qui laisse quasi instantanément un léger dépôt préjudiciable à l'adhérence de l'encre sur le cuivre.
Important : durant tout le processus d'élaboration du PCB, nettoyage compris, il est hors de question de poser les doigts sur le côté cuivre.
3°- Mordançage : c'est le "heureux hasard" dont je parlais plus haut :
Lire d'abord l'article «Peinture sur laiton».
-
sans attendre, dès que le cuivre est poli à la laine d'acier, tremper le PCB dans le bain de mordançage pendant 15 secondes ;
⇒ le cuivre prend un aspect mat, couleur "vieux rose".
-
sans poser les doigts sur le côté cuivre, rincer abondamment à grande eau ;
-
essuyer TRES délicatement avec un mouchoir en papier (pas de papier ménage qui est trop abrasif et qui dépose un très léger film de silicone).
4°- Préchauffage du PCB :
Le transfert de l'impression laser sera obtenu par refusion de la poudre qui viendra se coller sur le cuivre.
Cependant, la plaque de PCB a une inertie thermique importante vis à vis de celle du papier.
Pour favoriser l'adhérence de l'encre on préchauffe la plaque de PCB :
-
poser la plaque cuivrée sur une planchette en bois très plane, côté cuivre en l'air ;
-
poser par dessus un mouchoir en papier déplié puis replié simplement, pour éviter les sur-épaisseurs du pliage d'origine (pas de papier ménage) ;
-
poser le fer à repasser déjà chaud (réglage "coton") sur le mouchoir, sans appuyer et sans glisser ;
-
attendre 90 secondes (pour du Veroboard épaisseur 1,6 mm. Réduire le temps si le PCB est plus fin ou en bakélite). Ôter le fer et le mouchoir.

Attention : le PCB est TRES chaud. Si vous avez des gants légers, pensez à les enfiler pour manipuler la plaque aux étapes 4, 5 et 6.
5°- Transfert :
-
toujours sans attendre (pour éviter que la plaque refroidisse), disposer le typon sans appuyer au-dessus du PCB ;
-
poser le mouchoir en papier par dessus ;
-
déposer le fer sur le mouchoir, sans appuyer et surtout sans glisser ;
-
attendre 40 à 50 secondes (moins longtemps si le PCB est plus fin ou en bakélite).

6°- Laminage :
-
ôter le fer mais laisser le mouchoir ;
-
sans attendre, mettre en place le tube de cuivre au milieu de la plaque ;
-
poser dessus une planchette de bois et, en appuyant, faire rouler le tube de cuivre d'avant en arrière sur toute la longueur du PCB pendant une dizaine de secondes.
Grâce à cette manipulation, l'encre du typon imprimée sur le papier photo va être plaquée fortement contre le cuivre. Le PCB est chaud et l'adhérence de l'encre sera parfaite et rapide.

Utiliser un tube de cuivre (plomberie), propre et sans rayure.
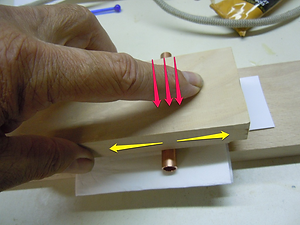
Rouler en appuyant, sur toute la longueur du PCB.
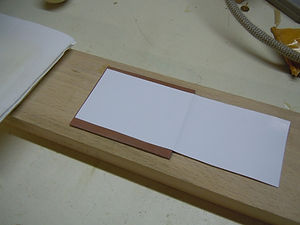
Au final le typon est correctement plaqué et il n'y a aucune cloque (bulle d'air).
Le laminage chasse les éventuelles bulles d'air prises entre le cuivre et le papier. La totalité de l'encre (je devrais dire "de la poudre") est mise en contact avec le cuivre et correctement transférée.
7°- Détrempage :
-
attraper l'ensemble PCB / typon par la partie de papier supplémentaire (fig. 1) ;
-
plonger l'ensemble dans de l'eau tiède (30 à 40° C) ;
-
attendre que le papier soit bien détrempé, jusqu'à ce qu'il présente des cloques sur toute la surface du PCB (fig.3).
N'hésitez pas à attendre plusieurs minutes. Le nettoyage en sera facilité et on limite le risque d'arrachage des pistes les plus fines.
8°- Nettoyage :
Plus le papier est détrempé, donc mou, plus le nettoyage sera réussi.
-
arracher délicatement l'excédent de papier ;
-
avec le pouce, frotter le circuit pour ôter le papier mouillé qui reste (fig. 4).
N'ayez pas peur d'insister.
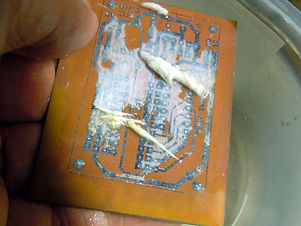
Fig.4
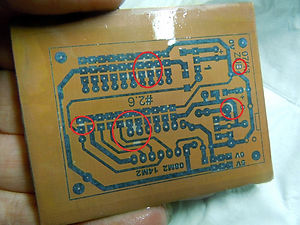
Fig.5
La figure 5 montre l'état du circuit en cours de nettoyage : des restes de papier s'accrochent toujours dans les trous de pastilles et dans les petits intervalles entre pistes et pastilles (cercles rouges).
-
insister avec le pouce.
En général cela ne suffit pas (Fig. 5).
Il faut alors utiliser une brosse à dents mi-dure (la brosse, pas les dents ) ; -
rincer abondamment le PCB.
Remarque : quand le PCB est mouillé il n'est pas toujours facile de voir les petits restes de papier dans les pastilles.
Essuyer le circuit et après quelques dizaines de secondes, ces restes de papier (s'il y en a) réapparaissent en blanc. Il suffit alors de mouiller de nouveau le circuit et de brosser les parties incriminées.
Note : si à ce stade, par malchance, le circuit présente des défauts majeurs (pistes et pastilles abîmées ou coupées, etc.), pas de panique : «aller directement à la case départ sans passer par les cases 9 et 10... et recommencez», comme au jeu de l'oie.
Sauf que là vous n'aurez pas de gage !
9°- Gravage :
Chacun utilisera la méthode et les produits dont il a l'habitude.
Personnellement je suis adepte de l'utilisation du mélange «eau + acide chlorhydrique + eau oxygénée à 130 volumes».
Cette méthode est décrite à la fin de l'article «Petite cuve de gravage des PCB».
La photo ci-dessus montre le résultat que l'on peut obtenir, avec un taux de réussite de l'ordre de 95% au moins :
-
les lettres "08M2 14M2" ont une hauteur de 2 mm ;
-
les chiffres "#2.6" mesurent 2,5 mm ;
-
les pistes mesurent 0,8 mm de largeur ;
-
les trous des pastilles carrées ont un diamètre de 0,5 mm.
Aucune piste ni aucune pastille n'est abîmée et même si sous la loupe le tracé est un peu moins "piqué" qu'avec une méthode classique (insolation...), avouez que le résultat est honorable.
10.- Élimination de la poudre plastifiée :
C'est l'étape la moins drôle.
Toujours avec la laine d'acier triple zéro (et beaucoup d'huile de coude) on ôte l'encre, qui est en réalité de la poudre plastifiée.
Si les étapes précédentes ont été correctement menées, la poudre plastifiée adhère fortement et son élimination demande de l'énergie.
On peut s'épargner quelques efforts en utilisant l'acétone pour enlever le plus gros. Opérer dans un endroit aéré.
Je vous recommande de passer ensuite une couche de protection sur votre circuit tout beau tout neuf : étamage à froid, paraffine (voir l'article «Bougie et térébenthine»), vernis soudable... afin de le protéger de l'oxydation.
Compléments :
Chacune des étapes décrites ci-dessus est importante et indispensable.
-
j'ai essayé sans le mordançage ⇒ ça ne marche pas.
-
j'ai essayé sans le laminage, en pressant seulement avec le fer à repasser ⇒ ça ne marche pas.
-
j'ai essayé sans préchauffer le PCB ⇒ ça ne marche pas.
En fait, ces trois étapes sont les clefs principales de la réussite.
Notes :
Les temps de préchauffage du PCB et de chauffage du typon sont dépendants du fer à repasser utilisé et de son réglage, mais aussi de l'épaisseur du PCB et de sa qualité (époxy ou bakélite).
Chacun fera son chronométrage personnel mais les temps ne devraient pas être très différents de ceux indiqués ci-dessus.
Bien entendu – mais faut-il le préciser – toutes ces manipulations devront se faire en évitant les poussières.

That's all Folk's
Ressources électroniques
bottom of page